There are three basic types of crushing machines, each with its own unique characteristics and strengths. HSI crushers, for example, use hammers to break up rock. The difference between a HSI and a cone crusher is in the degree of crushing. This allows the user to maintain tight control over the final product size and minimize waste. Read on to learn more about each type of crushing machine and which is best for your project.
HSI Crushers Break Rock with Hammers
An HSI crusher is a type of crushing equipment that breaks rock by impacting it with hammers. These crushers are available in various configurations, including stationary crusher plant for sale, trailer, and crawler versions. Originally used in soft materials such as limestone, gypsum, and other abrasive materials, HSI crushers are now used to crush hard rock and other non-abrasive materials as well.
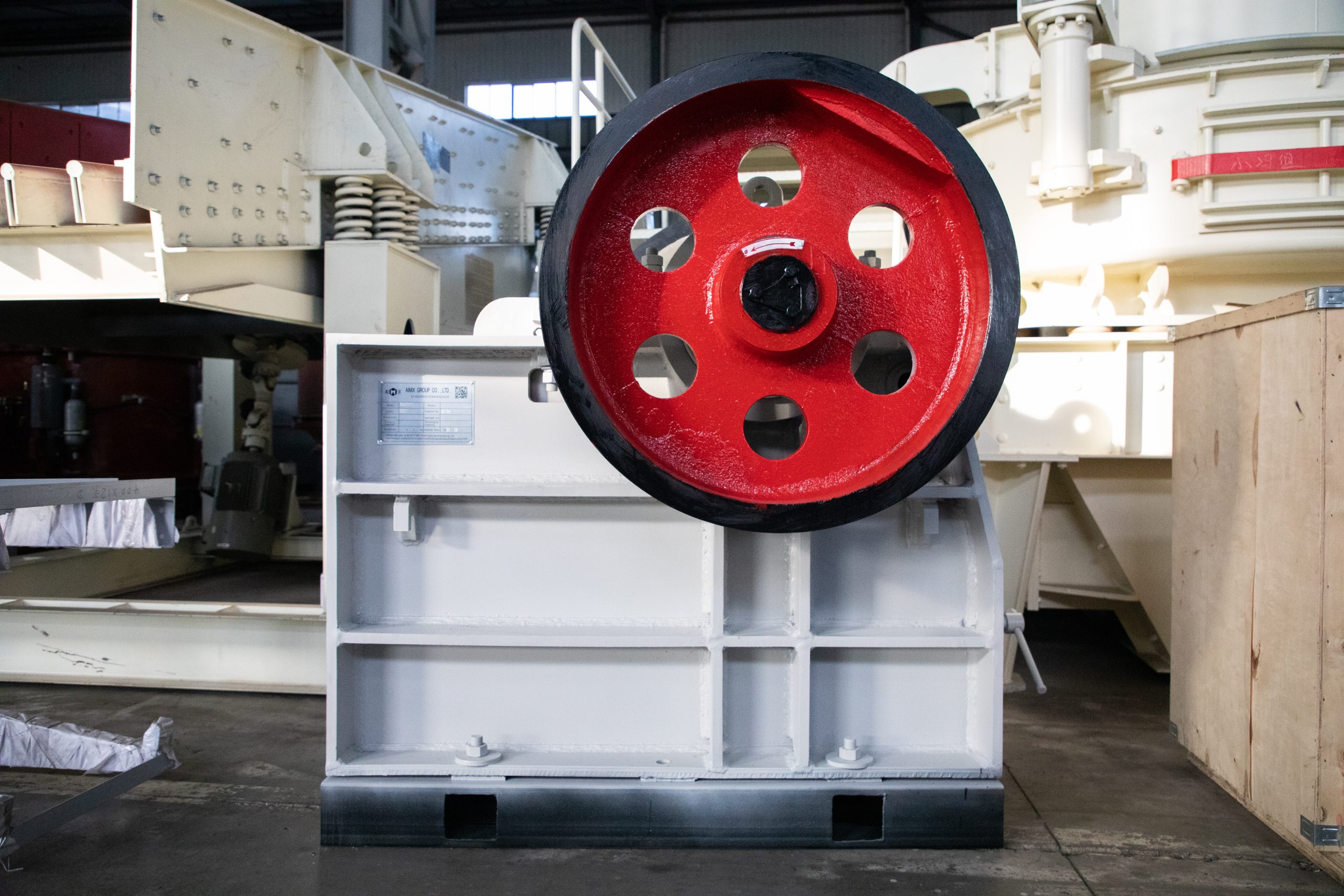
The HSI crusher uses a high-speed rotating rotor with wear-resistant tips and a crushing chamber to break rock. The hammers on the rotor assembly produce fractures that result in pieces of stone of varying sizes and shapes. Because of the low-profile design of HSI crushers, they have a limited expansion area above the rotor. As quarry shot enters the crusher, it impacts the hammers and strikes the curtains. The force from the impact fractures the stone along natural fault lines.
Cone Crusher
When it comes to cone crushers, there are several basic categories. The basic design hasn’t changed much in sixty years, but the speed at which the cones rotate is the primary factor that has changed. In 1960, a 48-inch cone crusher could produce 170 tons per hour of crushed rock. Today, that number has increased to more than 300 tons per hour, thanks to improvements in both crushing chamber design and rotating speed.
The mantle throw of a cone crusher for sale is based on the material entering the crushing chamber. Adjusting the distance between the mantle and concave determines how fine a product will be, but it can also reduce the energy needed to process a load. Some cone crushers offer closed-side setting adjustment, which is done by tightening a bonnet on the top of the crusher. This feature allows the operator to adjust the closed-side setting to obtain the ideal product size.
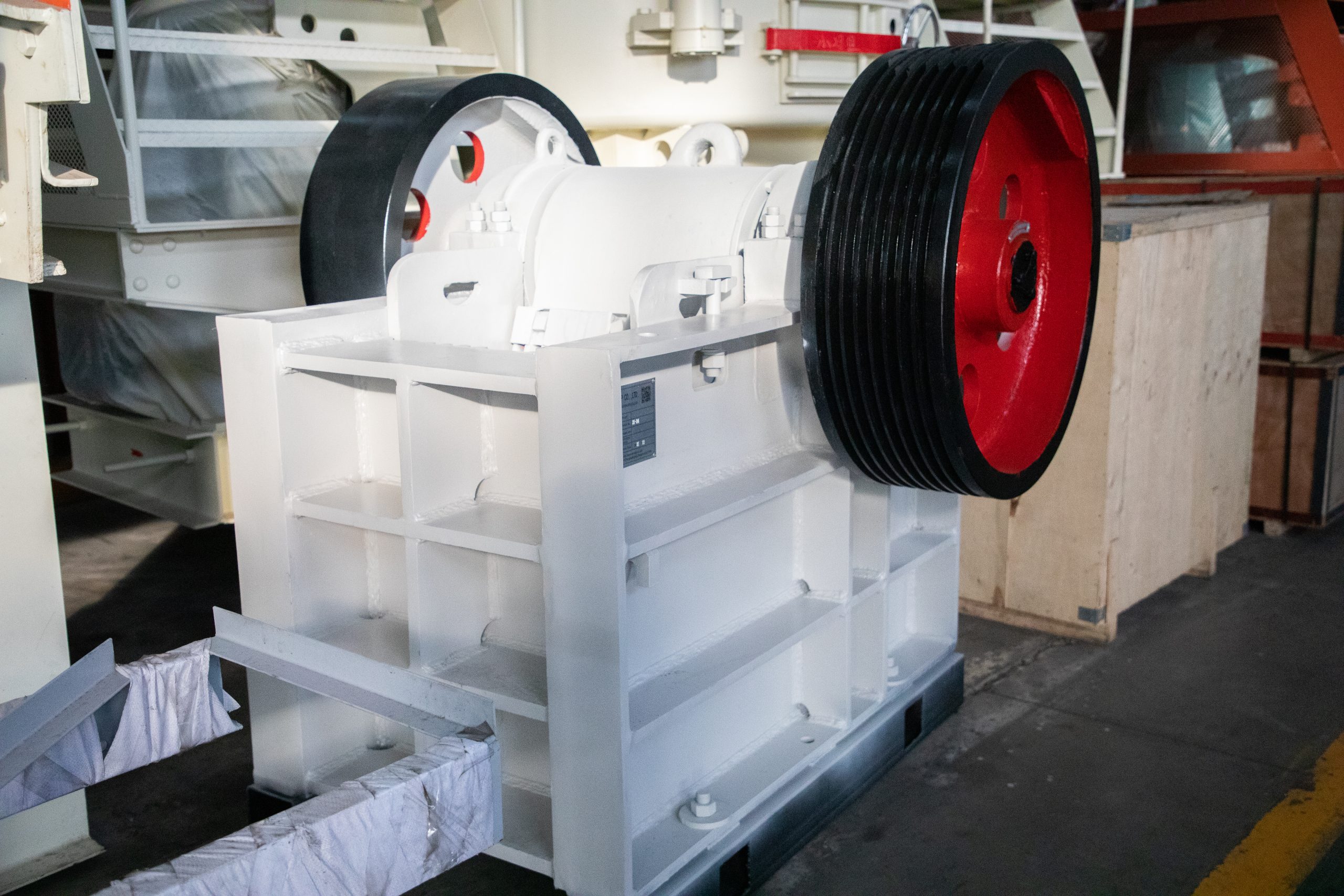
Impact Crusher
There are two general types of impact crushers: compression and impact. Compression crushers squeeze materials until they break, while impact crushers use quick impacts to crush material. Both jaw and impact crushers are used in mining, construction, and other industries. They all operate on the same principle, but one has a better reduction ratio than the other. Impact crushers are typically cheaper than compression crushers. They are also more efficient than jaw crushers, as they break large stones and ores along natural lines.
The mechanical structure of an impact crusher is defined by the impactor, which is the primary instrument for breaking up materials. Impact crushers are comprised of a rotor set among anvils and plates. The anvils and plates bear the impact of materials being crushed, and they have openings that allow for the material to escape. Horizontal shaft impactors and vertical shaft impactors are both types of impact crushers. Both types of impactors are useful for crushing materials, and they come in several types.
Roller Mill
There are different types of crushing roller mills, each with their own benefits and disadvantages. For instance, a straight roller mill tends to produce more heat than a reduction mill. In any case, the crushing operation should not compromise the gluten and strach features of flour. Another benefit is that the roller mill can be set to a constant feeding speed, minimizing the risk of damage to the crush machine Malaysia. Lastly, the machines can be equipped with different sensors, such as loadcells and sensors, which can detect abnormalities before the failure.
Two-roller mills are the simplest type of mill, which crushes material between two rollers. Then, the crushed material moves on to its final destination. The operator can adjust the spacing between the two rollers for the desired particle size. Smaller pieces are produced when the rollers are closer together. This is the type of mill that is used for crushing grain, construction aggregate, cement, recycling, and other materials.
Hammer Mill
There are various types of hammer mills available. Nevertheless, the basic principle behind them all remains the same. They are used to crush various materials in various industrial applications. The most common types of hammer mills are ball mills, sizing grinders, and impact crushers. Each one serves the same purpose: to reduce the size of material. This article will discuss the various types of hammer mills and how they can be used for specific applications.
The main difference between hammer mills and other China crusher machines lies in their material-crushing mechanisms. Hammer mills use impact to break the material into small particles. Their blades may be flat or sharp. They rotate using a shaft that provides rotational power. Moreover, hammer mills have a screen that allows particles of a specific size to pass through it. A high-precision machine, a hammer mill is an excellent option for crushing materials with high-value materials, such as glass and ceramics.